Metal vs Aluminum Roofing – Differences, Pros and Cons, Benefits
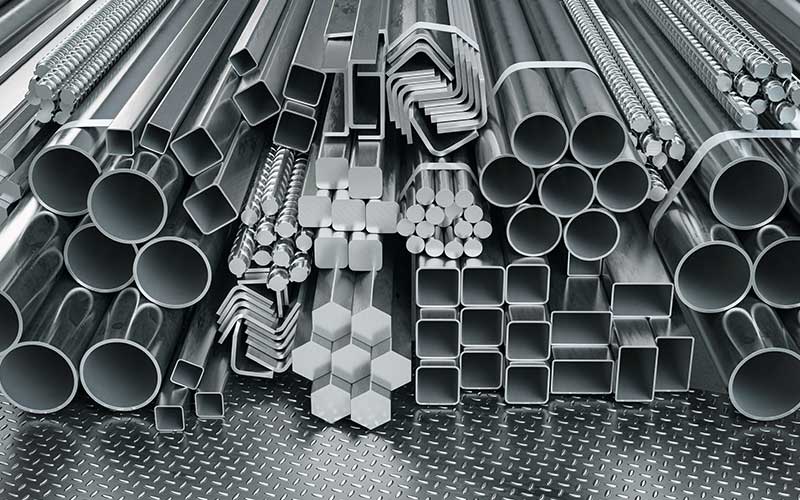
What Is a Steel Roof?
A steel roof is a weather-resistant structural covering system made from manufactured steel sheets or tiles, designed for long-term building protection and performance. While commonly grouped under “metal roofing,” steel roofing is distinct in its composition, weight, coating requirements, and structural strength. According to the Metal Construction Association (MCA), steel remains one of the most widely used metal roofing materials in the United States, with applications ranging from residential housing to large-scale industrial facilities due to its strength-to-weight ratio, affordability, and design versatility.
Unlike aluminum, which is corrosion-resistant by nature, steel requires a protective coating to prevent rust. The most common coatings are galvanized (zinc-coated) and galvalume (zinc-aluminum coated), both of which significantly extend the service life of the base steel. Stainless steel—an alloy containing chromium and nickel—offers corrosion resistance without external coatings but is typically reserved for high-end projects due to its elevated cost.
Steel roofing is generally manufactured into standing seam panels, corrugated sheets, or pressed metal shingles. In residential construction, it is most commonly used in 24- to 29-gauge thicknesses, with lower gauges indicating thicker and more impact-resistant material. These panels are installed over underlayment systems and fastened either through exposed or concealed mechanisms depending on the architectural requirement. When correctly installed, steel roofs can last between 40 to 70 years, with galvalume-coated panels often achieving longer performance due to superior oxidation resistance, particularly in humid climates.
The functional benefits of steel roofing are primarily rooted in its mechanical strength, making it particularly suitable for regions with severe weather, including hailstorms, high winds, and heavy snowfall. Steel also holds a Class A fire rating, the highest available, making it an ideal roofing option for wildfire-prone regions. Additionally, coated steel roofs reflect sunlight effectively, reducing attic temperatures and lowering cooling loads in summer months.
However, the use of steel roofing does present certain considerations. As a denser metal, steel is heavier than aluminum and may require more robust structural support on older or lightweight buildings. While coatings do protect against corrosion, steel roofs are still vulnerable in coastal areas with high salt content in the air. For these applications, aluminum is often preferred due to its natural resistance to oxidation. Furthermore, because steel expands and contracts more significantly with temperature changes than aluminum, fastening systems must be properly designed to account for thermal movement, especially in standing seam applications.
Steel generally offers a more affordable entry point into metal roofing than aluminum, with galvalume and galvanized systems being especially economical. Nevertheless, total installation costs can vary depending on thickness, coating, seam system, and regional labor rates. For many homeowners and commercial property developers, steel roofing represents a balance of structural durability, design flexibility, and long-term value when environmental conditions and proper detailing are accounted for.
What Is an Aluminum Roof?
An aluminum roof is a type of metal roofing system made from aluminum panels or shingles, selected for its lightweight properties, high corrosion resistance, and suitability in coastal and humid environments. While aluminum is less dense than steel, it forms a natural oxide layer upon exposure to air, making it inherently resistant to rust and eliminating the need for protective metallic coatings. According to the Metal Roofing Alliance, aluminum roofing is increasingly chosen in marine and high-salt environments due to this natural resistance, as well as its favorable strength-to-weight ratio.¹
Aluminum roofs are typically manufactured as standing seam panels, interlocking shingles, or modular tiles. These products are installed over decking with synthetic underlayment, and can either be mechanically seamed or fastened with hidden clips, depending on panel profile and design. Unlike steel, aluminum panels are almost always painted using high-performance coatings such as PVDF (polyvinylidene fluoride), which enhance UV resistance and preserve color in aggressive climates. The material is often used in gauges from 0.032" to 0.050", equivalent to approximately 24–28 gauge in steel, though comparisons are approximate due to differences in metal density.
Aluminum’s defining characteristic is its superior corrosion resistance, particularly in applications near oceans or large bodies of water. This makes it a common roofing choice in coastal homes, island developments, and tropical resort construction. Its natural resistance extends to acid rain and urban pollution, both of which can degrade other metals more quickly over time. In addition to this chemical durability, aluminum roofing offers structural benefits: it is lighter than steel by nearly 60%, which can reduce dead load on roof trusses and framing systems, especially valuable in reroofing older structures.²
In terms of longevity, aluminum roofing generally lasts 40 to 60 years, with some systems exceeding that timeframe when maintained properly. The absence of rust risk reduces the long-term degradation often seen with uncoated or poorly maintained steel systems. Aluminum roofs also hold a Class A fire rating and perform well under high wind conditions, with many systems rated for uplift resistance exceeding 120 mph. Like steel, aluminum is also a reflective material, offering energy savings when installed with “cool roof” coatings approved by ENERGY STAR® and the Cool Roof Rating Council.³
However, aluminum is not without its limitations. The material is softer than steel, making it more prone to denting under hail impact or falling debris. It also expands and contracts more than steel due to its higher thermal coefficient, which requires careful installation with floating clip systems to prevent warping or oil-canning in long panel runs. Additionally, aluminum’s higher material cost can be a barrier for some homeowners; in many markets, it is priced 20–35% higher than comparable steel roofing systems, particularly for embossed or textured finishes that hide visual imperfections.
Because aluminum is 100% recyclable and often made from high post-consumer content, it remains a preferred choice for sustainability-focused construction. Its light weight also lowers shipping emissions and reduces strain on installation crews, offering both environmental and practical benefits. For structures located in moisture-rich environments or where rust prevention is a top priority, aluminum is often regarded as the superior metal roofing material despite the price premium.
What Are The Differences Between Aluminium And Steel Roofs?
Does Aluminum Have Better Corrosion Resistance Than Steel Roofing?
Yes, aluminum has superior corrosion resistance compared to steel roofing. This distinction lies in the fundamental properties of the metals themselves. Aluminum forms a natural oxide layer when exposed to air, which immediately seals the surface and prevents further degradation. This self-protecting feature means aluminum does not require additional metallic coatings to resist rust, unlike steel, which must be coated with zinc (galvanized) or a zinc-aluminum alloy (galvalume) to delay oxidation.
In practical terms, this means aluminum roofing performs significantly better in high-moisture environments, particularly near oceans, lakes, or tropical climates where humidity and salt exposure are constant. Salt is especially corrosive to unprotected steel, rapidly breaking down coatings and accelerating rust formation. Galvalume-coated steel is more corrosion-resistant than galvanized steel, but it still falls short of aluminum’s natural resistance when exposed to salt air or acid rain over long periods. For this reason, aluminum is the preferred material in coastal applications and marine-adjacent construction zones.
Over time, aluminum’s passive oxide layer remains stable, even when scratched or damaged, while steel roofing systems can suffer from coating breaches that expose the substrate to oxidation. This distinction gives aluminum a practical longevity advantage in environments where protective coatings degrade more quickly due to weather, airborne chemicals, or mechanical wear. While both materials can last 40+ years with proper installation, aluminum tends to retain its integrity longer in coastal or corrosive settings without as much maintenance.
Another factor is recyclability and environmental behavior. Because aluminum’s corrosion resistance is intrinsic and not reliant on surface treatments, the material remains cleaner and more stable in long-term exposure, reducing the risk of leaching or runoff. This makes it a better choice for rainwater catchment systems and environmentally certified construction projects where material stability matters beyond basic function.
Which Is Heavier, Aluminum or Steel Roof?
Steel roofing is heavier than aluminum. Standard steel panels weigh between 1.5 to 2.0 pounds per square foot, depending on gauge and coating, while aluminum roofing typically weighs between 0.5 to 0.75 pounds per square foot. The difference in weight has direct implications for building structure, labor requirements, and long-term performance.
A lightweight aluminum roof places less stress on rafters, framing, and the building’s foundation. The reduced load is beneficial in retrofit applications, especially where existing structures were not engineered for heavy roofing systems. In seismic zones, or regions with aging infrastructure, the reduced weight can also lower the risk of structural failure. Lightweight panels are easier to transport, lift, and install, which can shorten installation times and reduce labor fatigue.¹
Steel’s added weight contributes to rigidity and structural mass, which can benefit projects where material movement must be minimized. Higher weight can improve performance under heavy wind conditions by reducing panel uplift. The density of steel may also dampen sound more effectively during rainfall. However, heavier materials increase the overall structural load and may require stronger support systems, which can raise construction costs or restrict use in lightweight or prefabricated buildings.²
Both materials are viable, but their mass must be considered in relation to the structural capacity of the building, the local climate, and the intended use of the roof system.
Is Aluminum More Expensive Than Steel?
Aluminum is more expensive than steel. On average, aluminum roofing systems cost 20% to 35% more than steel, depending on panel profile, finish, and regional availability. The higher price reflects both the material’s raw cost and the manufacturing process. Aluminum is more energy-intensive to produce, and its value as a corrosion-resistant, lightweight, and long-life roofing material is reflected in its market price.¹
Steel remains the more affordable option, especially in galvanized or galvalume-coated formats, which dominate large-scale residential and commercial installations. Thinner gauges of steel further reduce costs, though at the expense of impact resistance and long-term durability in aggressive environments. Aluminum, even at thinner gauges, resists corrosion without coatings and retains structural integrity over time, especially in coastal or humid climates.
For budget-conscious projects located in inland, dry regions, coated steel is often the better value. In contrast, aluminum may justify its premium cost in coastal, tropical, or high-humidity areas where exposure to salt or acid rain accelerates steel degradation. Over time, the lower maintenance demands of aluminum and its longer service life in corrosive environments can offset its higher upfront price.
Material cost is only one part of the total installed price. Aluminum’s lower weight can reduce structural support requirements and may simplify labor and logistics, offering cost savings elsewhere in the project. But as a baseline, when choosing between the two metals purely on initial material price, aluminum is consistently the more expensive roofing material.
Steel vs Aluminum Roof Strength
Commercial and residential metal roofing is primarily made of steel or aluminum. Both products are initially produced in giant rolls at a mill. All steel roofing has a protective barrier on both sides of the sheet called a metallic coating which protects against rusting. This is underneath and separate from any paint which imparts color to the product. There are two types of metallic coatings used: galvanized, which uses 100% Zinc in various thicknesses depending upon the product usage, and Galvalume, a mixture of aluminum and zinc. These metallic coatings “sacrifice” themselves to protect the iron in steel from oxidation when exposed to air and moisture. Zinc is a more “active” metal than iron so it oxidizes first and forms a protective barrier — zinc oxide, before the iron in the steel can become Ferric Oxide (rust). When zinc is combined with aluminum to form Galvalume there is even more protection in most circumstances.
Steel residential roofing is made in thicknesses designated by gauge and is generally 24 to 26 gauge, with the higher gauge being thinner than the lower. These gauges are appropriate since most residential metal roofing applications are over a solid substrate. Aluminum residential metal roofing is designated by decimal thickness and ranges from .023 to .040 thickness.
Density of Steel vs. Aluminum Roof
Steel is significantly denser than aluminum. The typical density of carbon steel is approximately 7.85 g/cm³, while aluminum has a density of about 2.70 g/cm³. This means steel is nearly three times heavier than aluminum when measured by volume.¹
In roofing applications, this difference directly affects material weight per square foot. Steel roofing panels generally weigh 1.5 to 2.0 pounds per square foot, depending on gauge, whereas aluminum roofing panels weigh between 0.5 to 0.75 pounds per square foot. Although both materials can be engineered to similar thicknesses and profiles, the intrinsic density of the base metal remains a defining factor in the overall weight and structural load of the finished roof system.
Density influences how the material performs under stress, how it is supported by roof framing, and how it is handled during transport and installation. Steel’s higher density contributes to its rigidity and impact resistance but also increases the static load on the building. Aluminum’s lower density allows for easier installation and reduced structural demand, making it especially suitable for re-roofing projects or lightweight framing systems.
While density does not determine strength or longevity on its own, it remains a key technical property when evaluating roofing materials for structural compatibility, handling requirements, and building code compliance.
Denting on Metal and Aluminum Roofing
Aluminum is more prone to denting than steel. The softer composition and lower density of aluminum make it more susceptible to surface deformation under impact. In roofing systems, this means that aluminum panels are more likely to show visible dents from hail, falling branches, or foot traffic during maintenance.¹ Steel, particularly in thicker gauges or high-tensile formats, resists denting more effectively due to its higher hardness and structural rigidity.
The extent to which a material will dent depends on several factors beyond metal type alone. Panel thickness, profile shape, fastening method, and the presence of underlying support all contribute to impact resistance. For example, standing seam panels with striations or embossed patterns are better at masking minor dents, especially in aluminum systems. Smooth panels without texture, often used in architectural aluminum applications, are more likely to show cosmetic flaws.
Steel panels—especially those made from G-90 galvanized or galvalume steel in 24 or 26 gauge—tend to hold their shape better after impact. In high hail-risk regions, steel roofing is often recommended due to its superior resistance to puncture and visible denting. Insurance providers in hail-prone areas may even offer premium reductions for installations that meet UL 2218 Class 4 impact resistance, a rating more commonly achieved by steel than aluminum.²
While aluminum may dent more easily, it does not corrode at the dent site, whereas a deep impact on steel could breach the protective coating and expose the substrate to oxidation if not properly sealed. For this reason, denting is not only an aesthetic concern but, in the case of steel, may have longer-term implications if left untreated.
Denting is a performance consideration that should be evaluated alongside climate, building use, and aesthetic expectations. In environments with minimal physical impact risk, aluminum's susceptibility to denting may not be a limiting factor. In harsher settings, steel’s resistance to deformation offers functional and visual durability.
What Are The Benefits Of Aluminum vs Steel Roof?
Steel and Aluminum Performance
Steel and aluminum both perform well as a metal roofing material. However, aluminum roofing, depending upon the exact product chosen, can run up to 20 percent higher in price compared to steel roofing. Aluminum is extremely resistant to corrosion caused by seawater, while steel is a bit more susceptible to seawater damage over time. Consequently, the warranties offered on the coil’s coating will be different as well. Both steel and aluminum perform pretty much the same, but the finish warranty for “coastal” areas is not provided for the steel panels. This is because of the potential for the coating to separate from the metal substrate at the edges, creating rust in environments that are near bodies of salt water. Exposure testing, however, has proven that Galvalume is up to three times more effective in preventing rust than galvanized steel material.
Aluminum is also lighter than steel if weight is a critical factor in determining the roofing material for your project. Both materials are very lightweight in comparison to other materials including asphalt shingles. Steel roofing is very lightweight with the heaviest product weighing about 1.5 pounds per square foot when installed. But aluminum is usually the lightest metal used for roofing. Its strength-to-weight ratio is among the highest of the “common” metals–that’s why airplane designers use aluminum for air frames. This lightness and thinness also means aluminum roofing material stores very little heat and also becomes cool quickly once it stops receiving direct sunlight.
Aluminum is more malleable than steel, allowing it to be configured into more complex profiles. However, especially in simpler profiles, you need fairly heavy gauge aluminum and that will boost its cost.
Steel inherently has more strength than aluminum, it’s usually less expensive and it’s more fire resistant without underlayment. Aluminum does not have a Class A fire-rating but the system can achieve a Class A rating with the proper underlayment and sheathing.
Both metal roof types will probably outlive all of us. Compared to traditional roofing materials, both offer a much longer lifespan, better environmental sustainability, better strength and a lower long-term cost. Steel can usually withstand winds of 110-150 mph and the material design of some steel roofs meet Miami-Dade and Florida Building Code requirements for hurricane wind uplift resistance.
Noise from rain, snow and small hail stones isn’t an issue for aluminum or steel roofing material–no more than it is for a shingle roof. That’s because it’s the sheathing and underlayment below the roofing material—on any roof—that blunts nature’s noises—not the roofing material itself.
Coatings for both aluminum and steel metal roofing coils come in a wide variety of standard colors and can be customized to meet the owner’s request. Custom colors generally cost more and certain coatings are more durable than others. For example, a Kynar PVDF coating offers additional protection against corrosion and oxidation.
Both aluminum and steel are two of the best energy efficient roofing materials. Both naturally reflect light and emit heat. Most aluminum and steel roofing material is available with cool roof coatings that meet LEED compliancy.
Ultimately, the needs of your project are going to dictate which you use. If the project is near the ocean and not in hurricane territory, the choice will probably be aluminum. If you’re out West building a wide-span storage building and brushfires are a concern, you’ll probably want to go with steel. If your concern is the added weight of a metal roof being retrofitted over an old shingle roof on an existing building, then you may want to think aluminum or a light gauge steel. Tap the metal that best meets your needs.
What are the Advantages of Metal roof when compared with Aluminum Roof?
- Greater impact resistance due to higher material rigidity
- Lower material and installation costs in most markets
- Reduced thermal expansion and better structural support over long spans
What are the Advantages of Aluminum Roof when compared with Metal roof?
- Inherent corrosion resistance without coatings, ideal for coastal or marine climates
- Significantly lower weight, reducing structural load and easing installation
- Long-term performance stability with minimal maintenance requirements
Does metal roof coating come in different colors?
Yes. Metal roof coatings come in a wide variety of colors and finishes. PVDF (Kynar 500®) and SMP coatings are the most commonly used systems, offering fade resistance, UV protection, and long-term color stability. Manufacturers typically offer both standard and custom color palettes, allowing alignment with architectural design and local aesthetic preferences.
What is the best gauge of metal roofing?
For residential roofing, 26 and 24 gauge panels are commonly used. 24 gauge provides greater rigidity, better wind uplift performance, and improved dent resistance—especially in standing seam systems. Thinner 29 gauge is used in low-budget or agricultural applications but is more susceptible to deformation under impact or load. The best gauge depends on structural needs, panel type, and environmental conditions.
Can a metal roof withstand heavy winds?
Yes. Most modern metal roofing systems, when properly installed, are engineered to resist wind uplift pressures ranging from 120 to over 150 mph, depending on the fastening system, panel profile, and roof geometry. Standing seam systems and interlocking panels offer some of the highest wind ratings and are frequently used in hurricane-prone regions with strict building codes.