Galvanized vs Galvalume Roofing: Difference, Pros and Cons, and Benefits
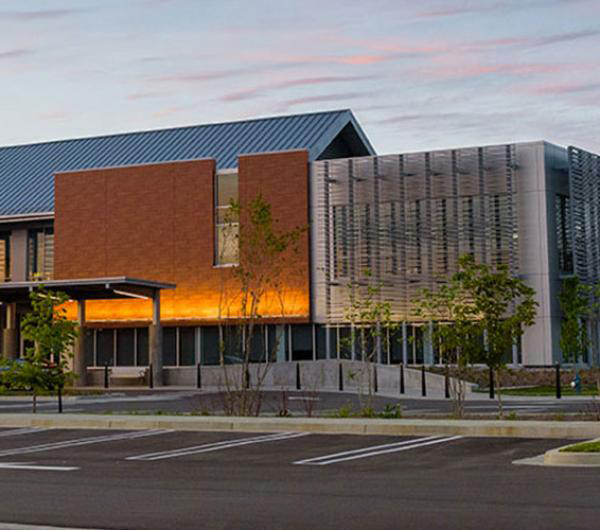
Galvanized vs Galvalume Roofing: Difference, Pros and Cons and Benefits
What Is Galvanized Roofing?
Galvanized roofing is a form of metal roofing made from galvanized steel, a material designed for enhanced protection against corrosion and rust. The steel is coated with a layer of zinc through a hot-dip process, where sheets are submerged in molten zinc to create a durable metallurgical bond. This coating shields the base metal from moisture and oxygen exposure, which are the primary causes of oxidation.¹ The presence of zinc ensures that galvanized steel not only resists environmental degradation but also continues to protect the underlying metal even if the surface is scratched or worn over time.
The durability of galvanized roofing is closely tied to the thickness of the zinc coating. Galvanized steel roofing typically lasts between 20 to 50 years depending on environmental exposure, maintenance practices, and the severity of weather conditions.² In climates with moderate humidity and low salt concentration, galvanized metal roofs provide reliable rust prevention and structural integrity with relatively low upkeep requirements.
Affordability is another advantage of galvanized steel. It remains one of the most cost-effective metal roofing options available, making it widely used in residential, agricultural, and light commercial construction. Painted finishes are often applied over the zinc layer to add UV resistance and expand aesthetic choices without compromising the protective properties of the metal.
In high-salinity environments, such as coastal regions, galvanized roofing may face accelerated degradation, as the protective zinc layer can corrode under persistent salt exposure. In such cases, alternative materials like galvalume or aluminum are preferred for their superior corrosion resistance in marine conditions. Despite this limitation, galvanized steel remains a trusted and proven material for roofing systems where cost, strength, and moderate climate resilience are primary project considerations.
What Is Galvalume Roofing?
Galvalume roofing is a type of metal roofing made from steel that is coated with a specialized aluminum-zinc alloy. The galvalume coating was invented in the 1960s by Bethlehem Steel as an improvement over traditional galvanization, offering superior protection against rust, corrosion, and weathering.¹ The coating consists of approximately 55% aluminum, 43.5% zinc, and 1.5% silicon by weight, combining the rust-resistance of aluminum with the sacrificial protection of zinc.
The main function of the galvalume coating is to shield the underlying steel from moisture, oxygen, and chemical pollutants. The aluminum component enhances corrosion resistance and provides heat reflection, while the zinc ensures that areas of exposed steel continue to resist rust even if the coating is scratched or worn. This combination allows galvalume to protect, withstand, and resist environmental degradation more effectively than traditional galvanized steel, particularly in a range of climatic conditions.
Galvalume material is widely recognized for its lightweight nature, making it easier to install and placing less stress on building structures compared to heavier roofing options. Its characteristic appearance is a silvery, spangled finish, although galvalume roofing panels can also be factory-painted in a variety of colors. Unpainted galvalume roofing maintains a reflective metallic sheen that contributes to excellent heat reflection, improving energy efficiency by reducing rooftop heat absorption.
Because of its aluminum content, galvalume roofing exhibits better long-term durability than galvanized steel in many environments. The typical lifespan of a galvalume roof ranges from 40 to 70 years depending on environmental exposure, installation quality, and maintenance. In inland or rural areas, galvalume roofs often outlast traditional galvanized systems, while in coastal environments with heavy salt exposure, performance may vary, and other materials like aluminum may be preferred.
What Are the Differences Between Galvanized and Galvalume Roofing?
Galvanized and galvalume roofing both use steel as the core material but differ in protective coatings. Galvanized steel is coated with pure zinc, providing sacrificial corrosion protection, while galvalume is coated with an aluminum-zinc alloy (55% aluminum, 43.5% zinc, 1.5% silicon) that enhances oxidation resistance and durability. Visually, galvanized roofing has a uniform, matte-gray finish, whereas galvalume features a more reflective, spangled surface. Weight is comparable, but galvalume typically offers greater longevity for its thickness.
In inland environments, galvalume outlasts galvanized steel by 10 to 25 years, while galvanized steel may initially resist corrosion better near coastlines before Galvalume's aluminum layer provides superior long-term protection. Material choice should consider climate, aesthetic goals, and budget priorities.
Corrosion Resistance Difference Between Galvanized and Galvalume Roofing
The corrosion resistance of galvalume roofing is generally superior to that of galvanized roofing under most environmental conditions. Galvalume’s aluminum-zinc coating protects the steel substrate by combining the sacrificial properties of zinc with the passive, long-term resistance provided by aluminum. The aluminum in the coating forms a tough, stable oxide layer that resists corrosion even after minor surface damage, significantly extending the material’s useful life.
Galvanized roofing relies solely on zinc to protect the steel. Zinc provides excellent sacrificial protection early in the roof’s lifespan, but over time, especially when exposed to acid rain, high humidity, or salt spray, the zinc layer can erode, eventually exposing the underlying steel to oxidation. In moderate and dry environments, galvanized roofing can perform reliably for decades. In humid or marine settings, the corrosion rate increases, and galvanized roofs generally require more maintenance or earlier replacement compared to galvalume.
Galvalume coatings are especially effective in resisting uniform surface corrosion and pitting corrosion, which are major concerns in metal roofing longevity. In independent tests such as salt spray and cyclic corrosion studies, galvalume consistently demonstrates two to four times the lifespan of standard galvanized steel under similar conditions.
Durability Difference Between Galvanized and Galvalume Roofing
The durability of galvanized and galvalume roofing depends largely on the type of coating, the environmental conditions, and the level of maintenance provided over the roof’s lifespan. Galvalume roofing generally offers greater durability than galvanized roofing because of its composite aluminum-zinc coating. The aluminum component protects the steel substrate by forming a stable oxide layer, which resists environmental degradation for a longer period than pure zinc alone. This resistance to oxidation, combined with the sacrificial properties of zinc, allows galvalume roofs to maintain their structural integrity for decades even under continuous exposure to moisture, UV radiation, and chemical pollutants.
Galvanized roofing, protected by a pure zinc coating, performs well initially but tends to experience faster surface wear over time. In dry, moderate climates, galvanized roofs can provide reliable durability, often lasting between 20 to 30 years depending on coating thickness and maintenance. However, the zinc layer is gradually consumed as it protects the steel, and once the coating is compromised through weathering or mechanical damage, the underlying steel becomes exposed to rust and corrosion.
Galvalume roofs generally achieve longer service lives, with many systems lasting 40 to 70 years under optimal conditions. Their durability is particularly notable in inland and industrial environments where oxidation and pitting are common threats to metal longevity. In marine environments, the presence of salt can shorten the life expectancy of galvalume compared to inland performance, but the material still typically outperforms galvanized roofing in terms of total lifespan.
When evaluated across a range of climates, maintenance practices, and installation conditions, galvalume roofing consistently demonstrates a higher level of durability and longer material stability than traditional galvanized steel. As a result, galvalume is often selected for projects where minimal maintenance and extended service life are critical considerations.
How Does Galvalume Compare to Galvanized Steel in Extreme Weather Conditions?
Galvalume roofing consistently outperforms galvanized steel when exposed to extreme weather conditions, particularly over long periods of environmental stress. The aluminum-zinc alloy coating on galvalume provides superior resistance to both uniform surface corrosion and localized pitting, two major forms of degradation accelerated by extreme climates.¹ The aluminum component forms a passive, self-repairing oxide barrier that shields the steel substrate from moisture, ultraviolet radiation, and atmospheric pollutants, even under continuous exposure to intense sun, heavy rainfall, or severe temperature fluctuations.
In regions prone to frequent freeze-thaw cycles, galvalume exhibits greater stability due to its ability to resist micro-cracking and coating separation, which are common points of failure in lesser coatings. The reflective properties of aluminum also help galvalume roofs manage solar heat gain more effectively, maintaining lower surface temperatures and reducing thermal stress on the building envelope. This ability to reflect rather than absorb solar radiation contributes to enhanced energy efficiency and slower material fatigue.
Galvanized steel, while providing good initial protection in moderate environments, tends to experience faster coating breakdown under extreme weathering. High temperatures, persistent moisture, and the presence of acidic or alkaline pollutants accelerate the consumption of the zinc layer. Once the zinc is depleted, the underlying steel becomes susceptible to rust formation, leading to a decline in both aesthetic and structural performance. In areas where hail is a frequent threat, galvanized steel’s higher surface hardness can offer slight advantages in dent resistance over thinner galvalume panels, but this benefit is generally outweighed by the superior corrosion performance of galvalume.
In coastal environments, neither material is immune to salt-induced corrosion, but galvalume shows better resistance during the early and middle stages of exposure. Over extended periods in highly saline atmospheres, even galvalume coatings may deteriorate, making full aluminum roofing a more reliable solution for marine applications.
Weight Difference Between Galvalume and Galvanized Roofing
The weight difference between galvalume and galvanized roofing is minimal because both materials use steel as the core substrate and only differ in the type of metallic coating applied. Steel has a density of approximately 7.85 g/cm³, and the thin coatings of zinc or aluminum-zinc applied during manufacturing do not significantly alter the overall mass of the roofing panels.¹ As a result, galvalume and galvanized steel panels of the same gauge and profile have virtually identical weights per square foot.
Standard roofing panels made from either material generally weigh between 1.0 to 1.5 pounds per square foot, depending on the thickness and design of the panel. In structural applications, this weight allows for high load-bearing capacity without excessive stress on framing systems. The lightweight nature of both galvanized and galvalume roofing materials compared to traditional asphalt shingles or clay tiles is a significant advantage, enabling faster installation, lower transportation costs, and reduced structural reinforcement requirements.
While the aluminum component of galvalume suggests a potential for lower weight compared to pure zinc coatings, in practical application the difference is negligible. The coatings are extremely thin—typically measured in microns—and the core material remains the controlling factor for overall mass.²
When evaluating roofing projects where weight is a key consideration, both galvalume and galvanized steel provide similar benefits in terms of reduced structural load. Therefore, decisions between the two materials are driven more by differences in corrosion resistance, durability, and cost rather than by variations in weight.
Price Difference Between Galvalume and Galvanized Roofing
Galvalume roofing typically costs slightly more than galvanized roofing when compared on a per-square-foot basis. The price difference is primarily due to the composition and performance characteristics of the coating. Galvalume’s aluminum-zinc coating involves more complex processing and uses a higher-cost material base, particularly because aluminum is more expensive than zinc by weight.¹ This manufacturing difference results in galvalume panels usually being priced 5% to 15% higher than comparable galvanized steel panels of the same gauge and profile.
In practical terms, galvanized roofing remains the more affordable option for projects with strict budget constraints, especially for agricultural, utility, and low-cost residential applications where initial capital cost is a priority. Galvanized panels are widely available and have long-standing use in the construction industry, offering a cost-effective solution where moderate corrosion resistance is acceptable.
Galvalume panels, although modestly more expensive, offer longer service life, enhanced corrosion resistance, and improved thermal performance. This means that while the initial investment for galvalume roofing is slightly higher, the total life-cycle cost can be lower due to reduced maintenance needs and extended material longevity.² In regions with harsh environmental exposure—such as high humidity, acid rain, or industrial pollutants—the improved durability of galvalume often justifies the small additional upfront cost by delaying the need for repair or replacement.
Strength Difference Between Galvalume and Galvanized Steel
Galvalume and galvanized steel roofing products exhibit similar fundamental strength properties because both use steel as their core structural material. The underlying mechanical strength, including tensile strength and yield strength, is determined by the grade and gauge of the steel substrate rather than the type of metallic coating applied.¹ Therefore, in terms of structural performance under load, both galvalume and galvanized steel panels of equivalent thickness offer comparable capabilities.
However, differences emerge in terms of surface hardness and coating durability. Galvanized steel, coated exclusively with zinc, tends to have a slightly harder surface finish. This higher surface hardness can offer marginal advantages in resisting superficial dents and scratches during transportation, installation, or minor impact events such as hail. In applications where cosmetic surface integrity is critical, galvanized panels may show fewer minor surface deformations in the early years of service.
Galvalume coatings, composed of an aluminum-zinc alloy, provide superior corrosion resistance but result in a slightly softer surface finish compared to pure zinc coatings.² This difference is typically minor and does not significantly affect the material’s ability to resist structural deformation under wind uplift, snow loads, or other mechanical stresses. Galvalume’s strength advantage lies primarily in its ability to maintain the core steel's integrity over a longer period by offering better protection against environmental degradation, not in an increase in physical rigidity.
When evaluating the long-term strength performance of roofing systems, galvalume generally sustains its mechanical properties better than galvanized steel because its coating delays corrosion of the steel substrate more effectively. Galvanized steel, while initially similar in strength, is more prone to weakening over time as the zinc coating degrades and rust penetrates the base metal.
Which Material Handles Extreme Temperature Fluctuations Better: Galvalume or Galvanized Steel
Galvalume roofing generally handles extreme temperature fluctuations better than galvanized steel roofing due to its superior coating composition and thermal stability. The aluminum-zinc alloy used in galvalume coatings forms a highly stable protective layer that resists cracking, peeling, and degradation when exposed to repeated cycles of heating and cooling.¹ The aluminum content imparts enhanced flexibility to the surface film, allowing it to expand and contract with the underlying steel substrate without significant loss of protective function.
Galvanized steel, coated with pure zinc, offers good initial protection but exhibits a higher susceptibility to thermal fatigue over time. Zinc layers are more prone to micro-cracking under cyclical expansion and contraction, especially in climates where daily or seasonal temperature swings are extreme.² These micro-cracks can accelerate the deterioration of the coating, ultimately exposing the steel to oxidation and leading to reduced material lifespan.
In addition to coating integrity, galvalume’s reflective properties contribute to its thermal performance. Unpainted galvalume surfaces reflect more solar radiation than galvanized steel, resulting in lower surface temperatures during peak heat periods. This reduction in thermal absorption further decreases the magnitude of expansion and contraction stresses experienced by the roof system, contributing to a longer and more stable service life.
In environments where structures are subjected to frequent freeze-thaw cycles, rapid temperature swings, or intense seasonal variation, galvalume roofing offers better resistance to coating breakdown, preserves structural integrity more effectively, and requires less maintenance over time compared to galvanized steel.
Heat Resistance Difference Between Galvalume and Galvanized Steel
Galvalume roofing offers better heat resistance than galvanized steel roofing due to the properties of its aluminum-zinc alloy coating. The aluminum content in galvalume reflects a higher percentage of solar radiation compared to the pure zinc coating found on galvanized steel.¹ This reflectivity reduces the amount of heat absorbed by the roof surface, leading to lower surface temperatures during periods of high solar exposure. By limiting thermal buildup, galvalume roofs help decrease the magnitude of heat-related stresses that contribute to material fatigue and surface degradation over time.
Galvanized steel, while providing good corrosion resistance initially, has a lower solar reflectance index and absorbs more radiant heat. This results in higher surface temperatures during the daytime, increasing thermal expansion and accelerating the deterioration of both the coating and the underlying steel. In climates with high ambient temperatures or intense sun exposure, galvanized steel roofing systems can experience faster coating breakdown and greater rates of thermal fatigue compared to galvalume.
The difference in heat resistance also affects building energy efficiency. Structures with galvalume roofing tend to experience lower attic temperatures and reduced cooling loads because the roofing surface emits less absorbed heat into the building envelope.² This performance characteristic makes galvalume a preferred choice for energy-conscious construction, especially in regions classified as hot or arid by climate zoning standards.
Environmental Impact Difference Between Galvalume and Galvanized Steel
Both galvalume and galvanized steel roofing products have environmental impacts primarily associated with material extraction, manufacturing processes, coating application, and end-of-life recycling potential. However, galvalume roofing generally offers a slightly better environmental profile over its service life due to its superior durability and reflective properties.
Galvalume’s aluminum-zinc alloy coating extends the roof's lifespan by resisting corrosion and degradation for longer periods than pure zinc coatings.¹ This longer service life reduces the frequency of material replacement, manufacturing demand, and associated resource consumption, lowering the overall environmental burden. Additionally, the higher solar reflectivity of galvalume panels contributes to better thermal performance, helping to reduce building cooling loads and associated energy consumption. Structures with galvalume roofing may qualify for cool roof credits under green building standards such as LEED (Leadership in Energy and Environmental Design).²
Galvanized steel roofing, while durable in moderate environments, tends to require replacement or maintenance sooner, especially in harsh or corrosive conditions. Shorter product lifecycles result in increased raw material demand, higher embodied energy over time, and more frequent waste generation. The zinc production process, although efficient, is energy-intensive, and repeated coating and fabrication cycles over the life of a structure can add cumulatively to the environmental footprint.
Both galvalume and galvanized steel are recyclable at end of life, with recovery rates exceeding 85% in most industrialized countries. However, galvalume’s longer functional lifespan typically delays the recycling stage, offering an environmental advantage by reducing the total number of manufacturing cycles needed over a building's service life.
In comparative lifecycle assessments, galvalume roofing systems demonstrate lower environmental impact metrics over a 50-year period when measured against galvanized steel systems of equivalent thickness and installation quality.
How to Choose the Right Roofing Material: Galvalume or Galvanized Steel?
- Galvalume offers better corrosion resistance and longer lifespan, typically 40 to 70 years depending on climate and maintenance.
- Galvanized steel is less expensive upfront and suited for moderate environments where extreme moisture or industrial pollution is not a major concern.
- Galvalume reflects more solar radiation, improving energy efficiency and reducing building cooling loads in hot climates.
- Galvanized steel provides slightly better initial dent resistance during installation but has lower long-term surface protection.
- For coastal, humid, or highly industrial areas, galvalume is preferred due to its superior resistance against atmospheric corrosion.
- For budget-sensitive projects with shorter expected service life requirements, galvanized steel remains a practical choice.
- Both materials are recyclable at end-of-life, but galvalume delays replacement cycles longer, offering better long-term sustainability.
How to Tell If Metal Is Galvanized
- Galvanized metal usually has a distinctive spangled surface pattern, appearing as irregular shiny or matte gray crystal-like areas.
- The surface texture of galvanized steel feels smooth but slightly grainy due to the zinc crystallization during the hot-dip process.
- Galvanized steel maintains strong magnetic properties because the underlying substrate is carbon steel.
- Over time, galvanized surfaces develop a dull, chalky patina caused by the formation of zinc carbonate as the coating naturally weathers.
Applying a small drop of vinegar or diluted acid can cause mild bubbling on galvanized surfaces as the zinc reacts chemically, confirming the presence of the coating. - Compared to painted or bare steel, galvanized surfaces resist rust formation for much longer but will eventually show white oxidation (zinc oxide) before any red rust appears.
- The color tone of galvanized steel tends toward uniform light gray if weathered, and brighter, reflective silver if freshly coated.