Metal Roof Sheets and Coil
The metal and aluminum coil in Englert’s roofing products are made from the highest quality materials available. We hold our suppliers to the strictest of standards and employ a rigorous qualifying process in selecting new sources.
All of our metal roofing coil and sheets are produced with recycled material with at least 25 percent of the raw material coming from post consumer or post industrial scrap. With our world class paint line, we maintain fully integrated manufacturing capability, ensuring the highest level of quality control.
Color Chart
Englert is one of the few single-source metal roof manufacturers with an in-house paint line. Whether the design calls for a natural weathered appearance or bright, high-performance, full-strength fluorocarbon colors, we’ve got a color for every project.
Darth Black
Pitch Black
Bone White
Stone White
Sandstone
Sierra Tan
Dove Grey
Slate Grey
Charcoal Grey
Patina Green
Everglade Moss
Hemlock Green
Forest Green
Hartford Green
Slate Blue
Pacific Blue
Royal Blue
Sunnet Blue
Matte Black
Medium Bronze
Dark Bronze
Mansard Brown
Burgundy
Terra Cotta
Colonial Red
Deep Red
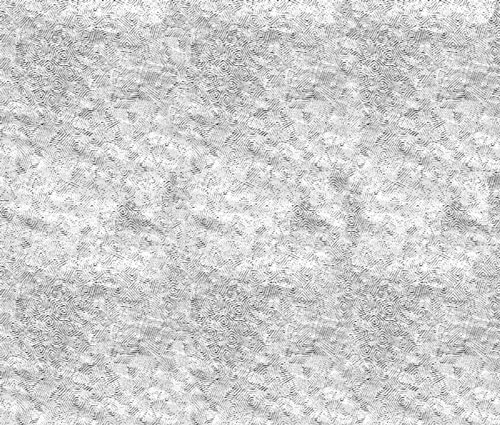
Galvalume-Plus(Mill Finish)
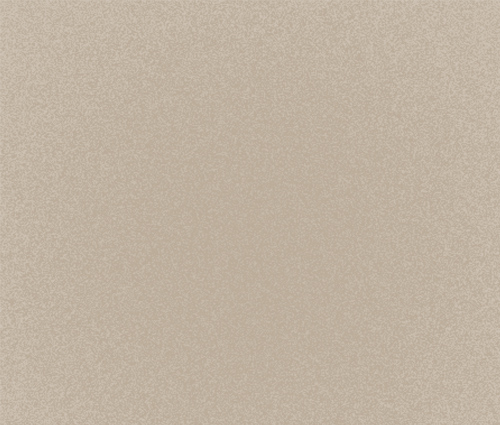
Champagne (Metallic)
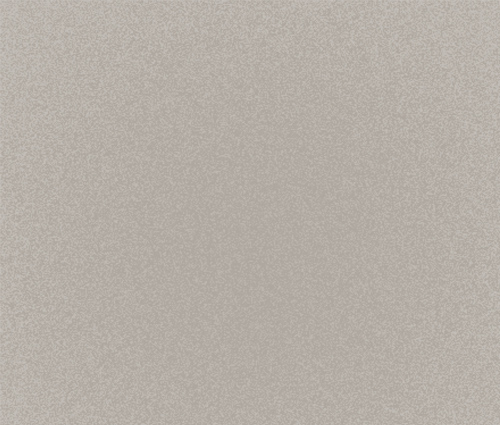
Preweathered Galvalume (Mill Finish)
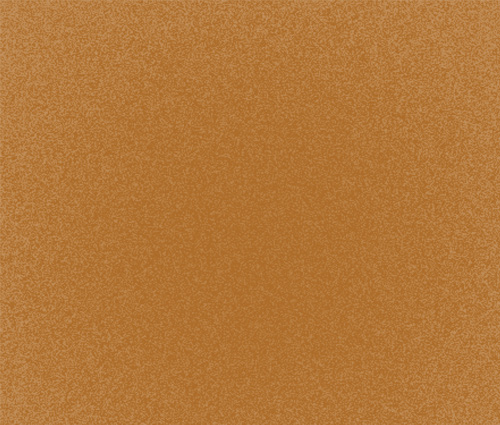
Copper (Metallic)
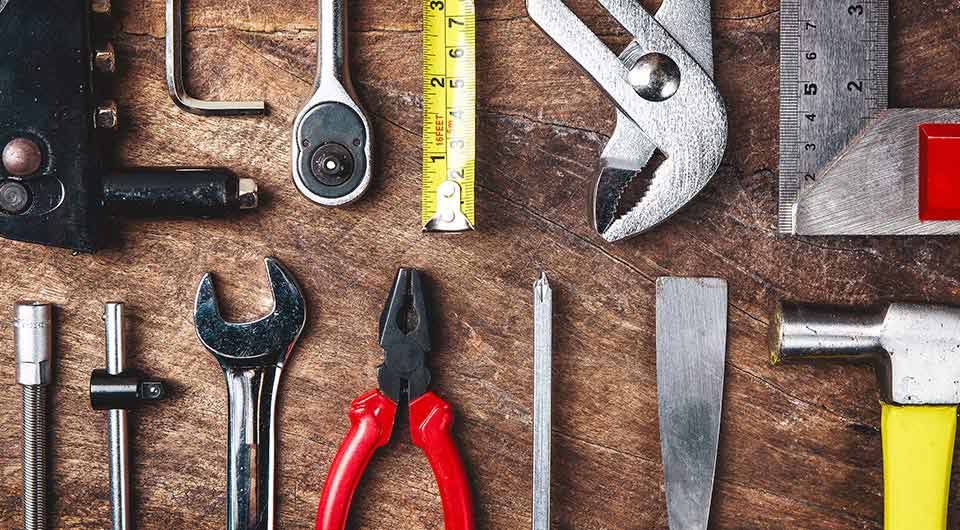
Resource Center
Stay ahead with the latest resources and insights on roofing coil.
View ResourcesView resources on metal roofing and gutter systems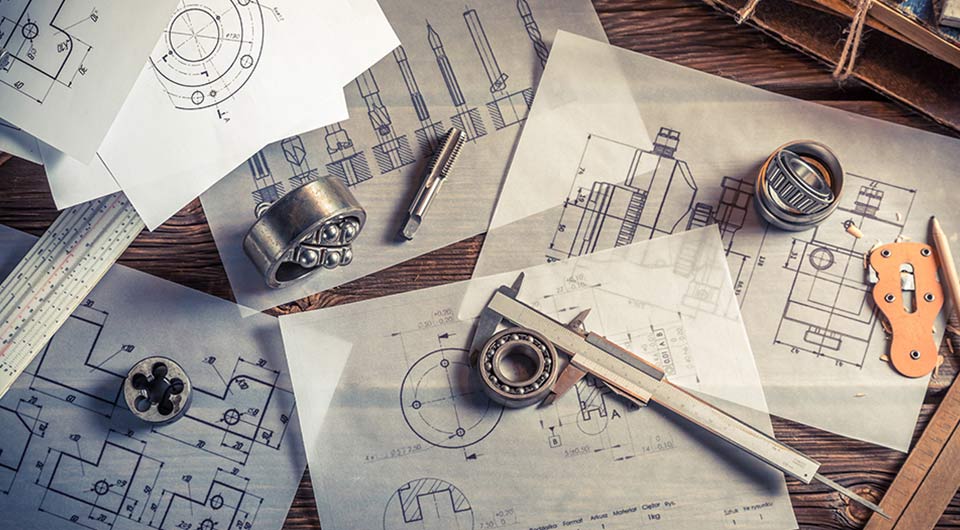
Catalogs
Access roofing coil catalogs, product sheets, brochures and materials.
View CatalogsAccess Englert product catalogs and brochures