Standing Seam Metal Roofing
Englert offers a wide range of standing seam metal roofing systems and panel profiles, widths, and finishes to meet any design objective. With our technically-advanced paint line, you can select any of our 28 ULTRA-Cool™ low-gloss, environmentally-friendly finishes.
All of Englert’s metal roofing systems are backed by stringent product testing, the best warranties in the industry, and engineering expertise.
Advantages to Metal RoofsLearn the advtanges to metal roofing systemsArchitectural Metal Roofs
Known for durability and strength, Englert’s architectural metal roofing systems are designed for use over a solid wood deck. They’re aesthetic in nature and chosen by architects for high visibility areas such as fascias, mansards, and other steep slope applications.
Architectural Metal Roofs
Known for durability and strength, Englert’s architectural metal roofing systems are designed for use over a solid wood deck. They’re aesthetic in nature and chosen by architects for high visibility areas such as fascias, mansards, and other steep slope applications.
Structural Metal Roofs
Our structural metal roofing systems are the industry's choice for use in open framing situations and are specifically designed for spanning roof purlins and rafters at various spacing.
Curved Panel Roofs
Englert's curved metal roofing systems provide the opportunity to incorporate the superior aesthetics of a curved metal design. We offer two curved metal roof systems designed to accommodate curved roofs, arched canopies, and walkway covers.
Curved Panel Roofs
Englert's curved metal roofing systems provide the opportunity to incorporate the superior aesthetics of a curved metal design. We offer two curved metal roof systems designed to accommodate curved roofs, arched canopies, and walkway covers.
Metal Roof Color Chart
Englert is one of the few single-source metal roofing manufacturers with an in-house paint line. Whether the design calls for a natural weathered appearance or bright, high-performance, full-strength fluorocarbon colors, we’ve got a color for every project.
Darth Black
Pitch Black
Bone White
Stone White
Sandstone
Sierra Tan
Dove Grey
Slate Grey
Charcoal Grey
Patina Green
Everglade Moss
Hemlock Green
Forest Green
Hartford Green
Slate Blue
Pacific Blue
Royal Blue
Sunnet Blue
Matte Black
Medium Bronze
Dark Bronze
Mansard Brown
Burgundy
Terra Cotta
Colonial Red
Deep Red
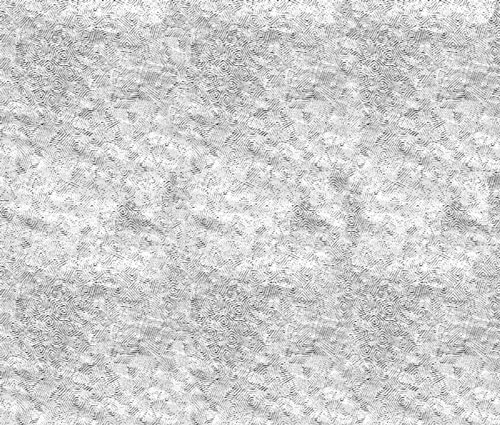
Galvalume-Plus(Mill Finish)
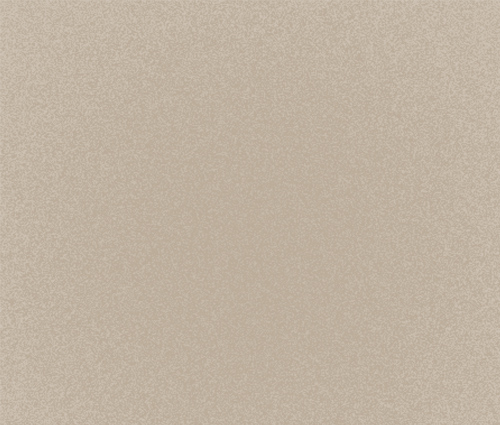
Champagne (Metallic)
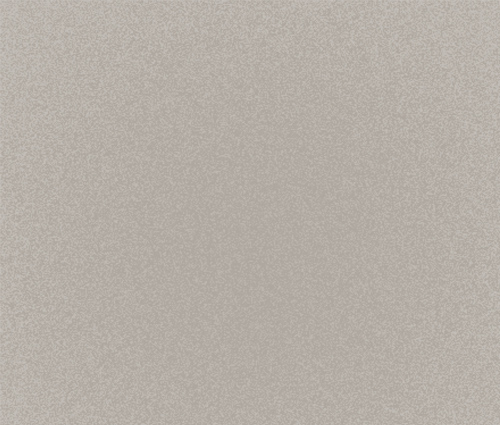
Preweathered Galvalume (Mill Finish)
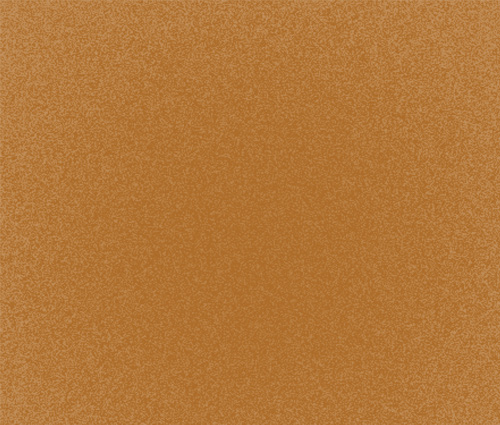
Copper (Metallic)
Metal Roof Visualizer
Want to see what your home or building will look like with one of our standing seam metal roofs? Englert’s visualizer design tool lets you personalize your project quickly and easily. Snap a picture of your home or building, then customize all aspects of the product to see how Englert can spruce up the look of any project. Our visualizer tool is built responsively so you can design anytime, anywhere, on any device.
Start DesigningSee how a metal roof will look on your building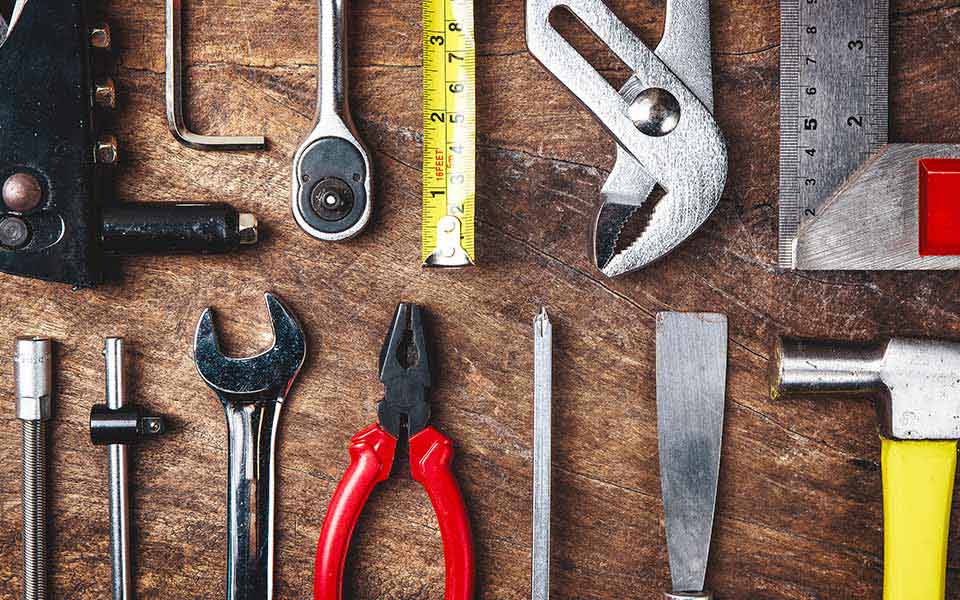
Resource Center
Stay ahead with the latest resources and insights on metal roofing.
View ResourcesView resources on metal roofing and gutter systems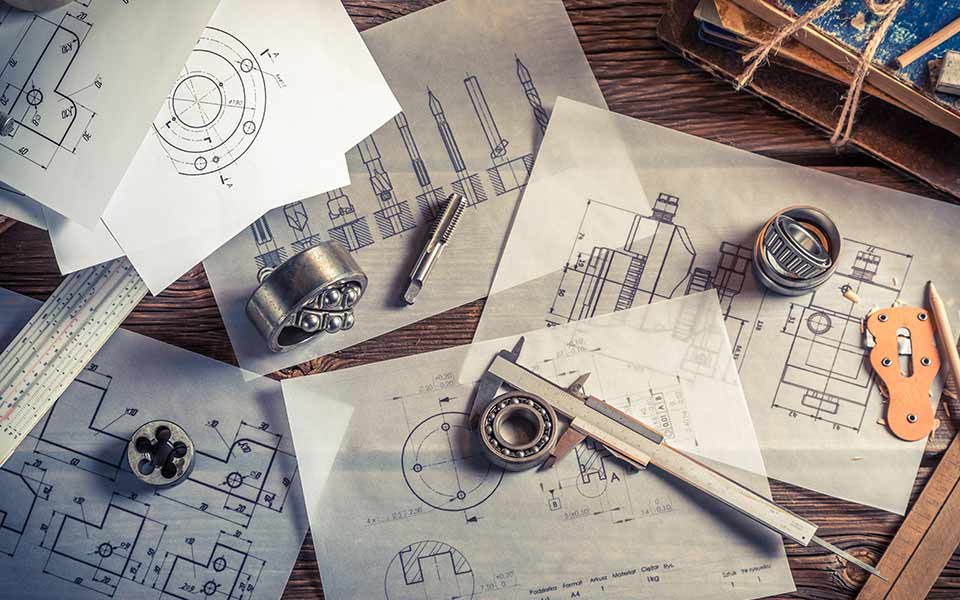
Roofing Catalogs
Access metal roofing catalogs, product sheets, brochures, and materials.
View CatalogsAccess Englert product catalogs and brochures