Roll Forming Machines for Metal Roofing
Englert brings metal roof manufacturing directly to the job site with our portable roll forming machines for metal roofing. On-site fabrication eliminates shipping damage, short shipments, and many sizing errors in addition to providing packaging and freight savings.
Our roll forming metal roofing machines are designed for experts in seamless gutter and metal roof installation. We offer a total package of support, including a mobile service force, machine training, testing, warranties, and engineering.
Metal Roofing Machines
Metal Roofing Machines
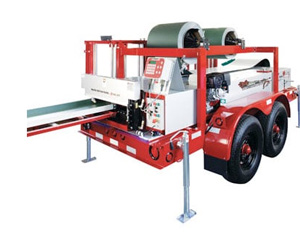
Multi-Panel Roofing Machine
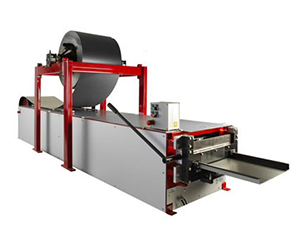
Fixed Panel FP1500/20
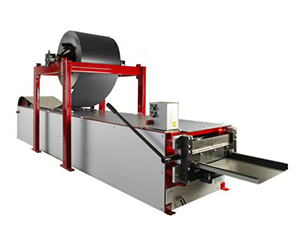
Fixed Panel FP1500/16

Fixed Panel FP1301/21
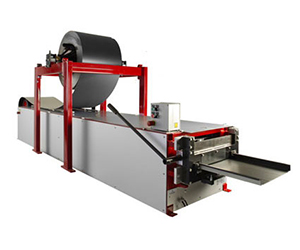
Fixed Panel FP1301/17
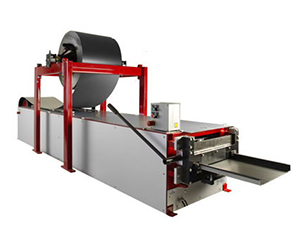
Fixed Panel FP1300/20
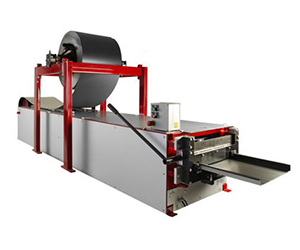
Fixed Panel FP1300/16
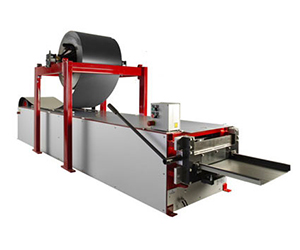
Fixed Panel FP1101/20
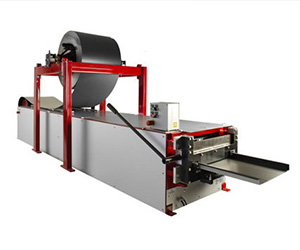
Fixed Panel FP1000/20
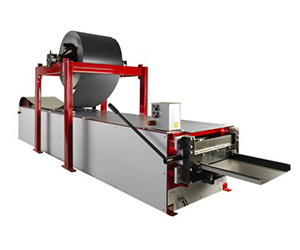
Fixed Panel FP1000/16
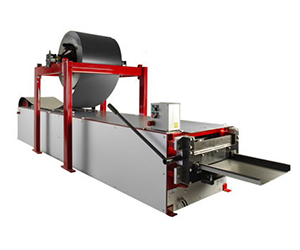
Fixed Panel FP1101/16
Panel Curving Machines
Panel Curving Machines
Electric Panel Seamers
Electric Panel Seamers
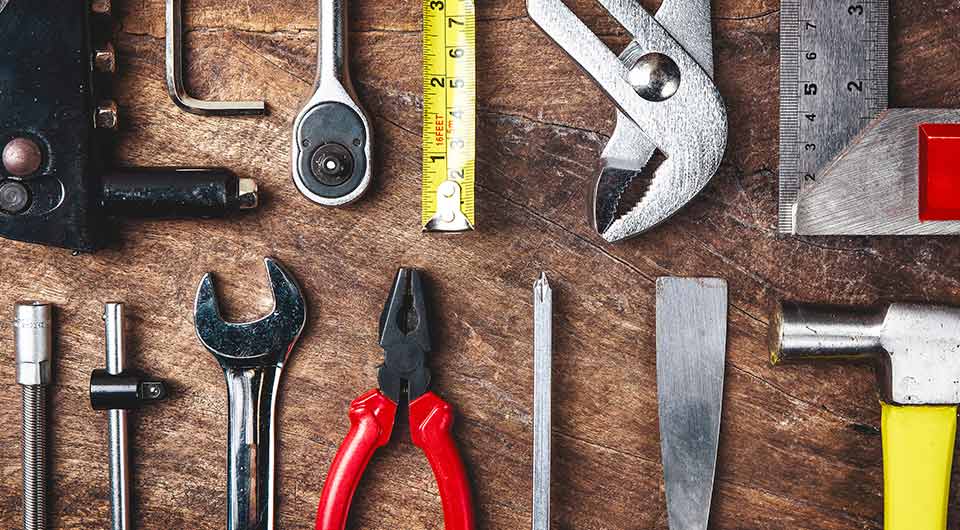
Resource Center
Stay ahead with the latest resources and insights on roll forming machines.
View ResourcesView resources on metal roofing and gutter systems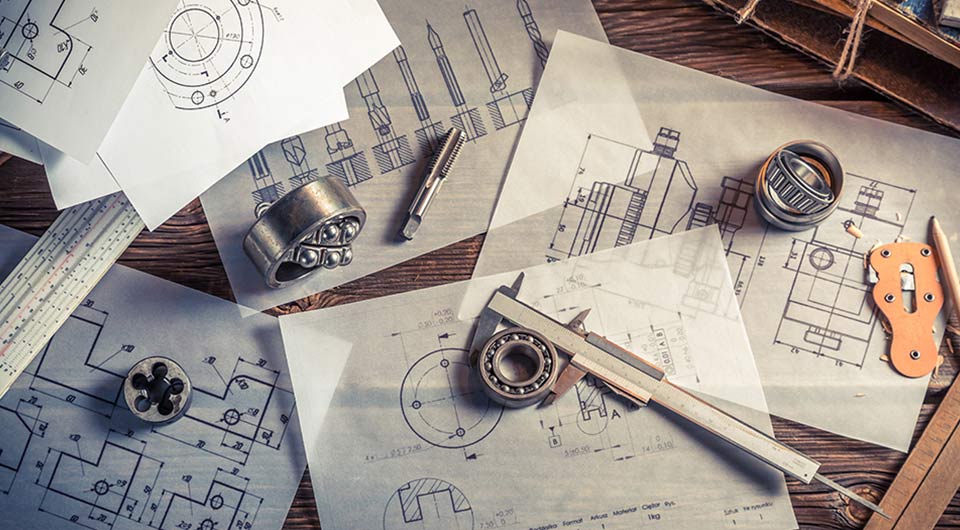
Catalogs
Access roofing machine catalogs, product sheets, brochures and materials.
View CatalogsAccess Englert product catalogs and brochures